Lamination on
extruded sheets with:
- Fleece
- Textile or fabric
- Foam
- Stripe(s)
- Decorative foil
- Logo-printed foil
- Removable protective foil
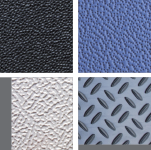
EXTRUDED SHEET
- Tailor-made materials for thermoforming
- Composite material – reinforcement with different fillers
- Wood-plastic/BIO composites PE & PP filled with nano-cellulose fibres
- Designed products fabric backed, metal-detectable, anti-slip, electroconductive grades, heavy filled and others
- Embossed surfaces: N1, N2, N3, ALU or on request
- Co-extrusion
Surface finishing:
- Glossy Mat
- Different textured structures
- with embossed rolls
Technologies:
- Extrusion of sheets (thickness 0.5–25mm, max. width 1,700mm)
- Co-extrusion (AB, ABA) of sheets (thickness from 1.2mm, max. width 1,500mm)
- Extrusion of sheets with direct compounding (thickness 1–10mm (max. width 1,600mm)
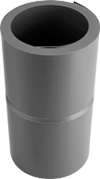
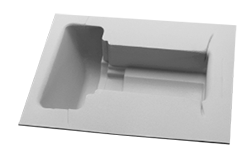
Others:
- Surface activation with flame treatment
- “Cut to size” parts from extruded sheets
Standard sheets in dimensions
2,000×1,000mm, 3,000×1,500mm
Thickness range
PE from 2mm to 25mm, PP from 2mm to 20mm
Maximum width:
1500 mm
Thickness: 1−8 mm
Colors: each layer different RAL
Rolls are available upon agreement.
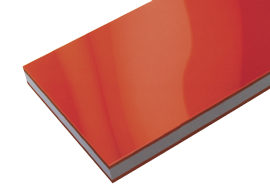
CO-EXTRUDED SHEET
The advantage of co-extrusion is that each layer imparts a desired property, such a stiffness, soft touch, environmental resistance, visual effect. Applications: automotive industry, food industry, luggage, … or similar.
Extruding two or more materials through a single die so that materials merge or weld together into a single structure before cooling allows the combination of different compatible materials and colors in a single sheet.
Filled materials
Fillers and additives are used to change and improve the physical and mechanical properties of plastics. In general, reinforcing fibers increase the mechanical properties of polymer composites while particular fillers of various types enhance a particular property.
Some of the main reasons to using fillers are:
- Improved mechanical properties
- Density control
- Thermal conductivity
- Optical effects
- Flame retardantcy
- Cost reduction
- Electrical properties; antistatic
Fillers and additives
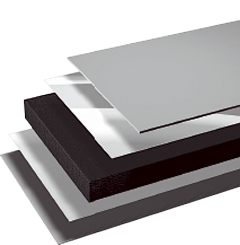
Key Benefits
- Visual appearance (special effects, color matching)
- Dimensional stability
- Shrinkage
- Stiffness
- Abrasion surface
- Weather influence resistance ( UV resistance,…)
- Controlled flammability
- Antistatic characteristics and electrical conductivity
- Controlled impact strength at lower temperature
Modification of basic polymeric materials with fillers:
- Talcum
- Wollastonite
- Calcium carbonate
- Short/long glass fibers
- Barium sulphate
- Wood flour
- Carbon black